Insert Molding
Scale Your Production with Expert Insert Molding Solutions
When managed by an expert, Insert Molding Solutions can streamline production, reduce costs, and enhance the strength and durability of your plastic components. This process involves inserting a pre-formed non-plastic part, like metal terminals or threaded inserts, into the mold and injecting thermoplastic resin around it to create a single, robust piece.
Insert Molding Solutions are perfect for low-volume production, bridge tooling, and prototyping. Industries like medical rely on these solutions to manufacture lighter, more durable end-use products.
At Omega Plastics, our team of insert molding experts employs both horizontal and vertical injection molding presses, offering versatile and flexible solutions to meet your manufacturing needs.
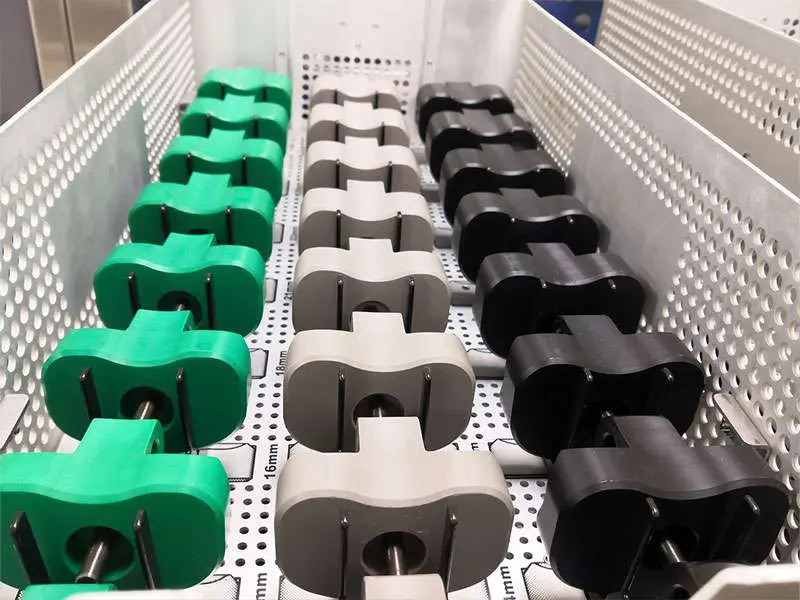
Advantages and Applications of Insert Molding Solutions
Advantages
- Eliminate Assembly Steps: Parts are joined during manufacturing, reducing labor costs.
- Enhance Durability: Internal components are protected by the outer plastic shell, resulting in products that withstand wear and tear.
- Efficiency Improvement: Replacing metal with plastic decreases weight, ideal for medical and transport applications.
- Meet Tight Tolerances: Precise manufacturing meets strict requirements, perfect for complex designs.
Applications
The versatility of molding solutions makes them invaluable in applications demanding strength, durability, and precision. In the medical field, products like surgical tools, lab equipment, and prosthetics benefit from this process. Other industries such as aerospace, automotive, and consumer products also find insert molding advantageous for scaling production and creating identical parts efficiently.
Partner with an Expert for Superior Plastic Parts
Insert molding may appear simple, but factors like material resistance to high temperatures and maintaining insert stability are critical. An expert will optimize mold design to minimize defects and enhance efficiency.
With over 30 years of experience, Omega Plastics offers tailored Insert Molding Solutions, ensuring collaboration and transparency throughout the process. Contact our engineering team today to learn how we can support your next project.
Flexibility for Your Success
Get in touch to learn how we can support your plastics needs.